Jean-Pierre Fréry at the head of a 3-person crew is getting ready to set off on a non-stop round-the-world voyage via the 3 capes on a production catamaran ( see our presentation of the Cavok project ). For this purpose he acquired a Lagoon 400 S2 which has just been delivered to him in Saint-Gilles-Croix-de-Vie. This n°544 of the series is one of the last built. Indeed, the Lagoon shipyard launched a new Lagoon 40 at the Cannes boat show in September 2017, which will replace it.
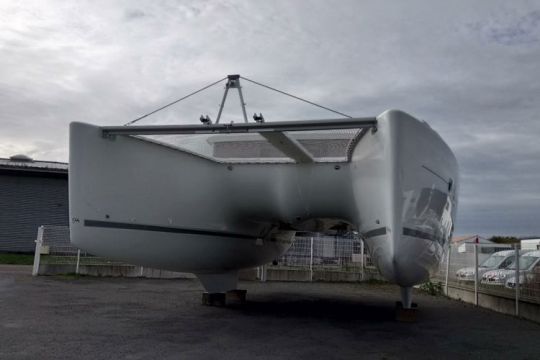
Cavok (this is the name of the Lagoon 400 S2) was not built as a prototype, but as a production boat. On board, you'll find all the usual facilities on this type of catamaran. Only certain recommendations have been requested from the shipyard in order to optimize Cavok's reliability and safety.
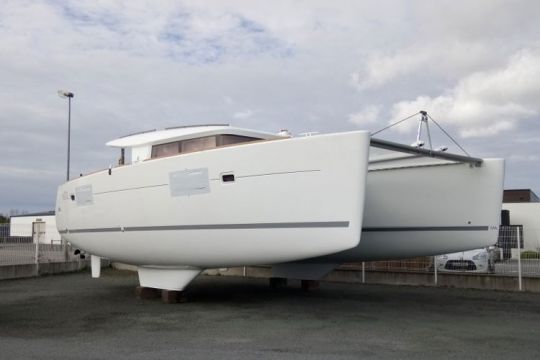
Indeed, five months at sea, a good half of them in particularly inhospitable waters, call for some precautions, especially with regard to watertightness. The most visible modifications are the absence of a hull porthole to illuminate the cabins. These have not been cut into the hull so as not to weaken it. Also noteworthy is the installation of watertight bulkheads at the bow and stern, which are not fitted as standard. For the rest, the construction is standard with only a care taken with the glues, some reinforcements at the level of the fixing points such as the spinnaker pulleys or the cleats (these will be used to hang the trailing boats to slow down the boat in heavy seas).
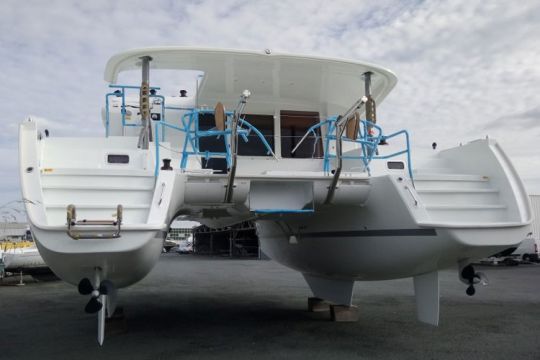
Other arrangements are more related to performance, such as preparing the hull for the small onion or fitting a steerable bowsprit to facilitate the installation of the spinnaker downwind.
Otherwise, the Lagoon 400 S2 is strictly standard. The mast for example is the standard model, the shrouds and chain plates are not reinforced..
Here is the complete list of the work carried out on board for this rather special "cruise":
Watertightness :
- Foaming of the front and rear bulkhead PVC pipes
- Deburring calibration and double bead of glue when assembling survival panels
- Mounting of 50 mm hutches equipped with bellows for the passage of bar lines in the aft bulkhead
- Installation of bulkheads and modules in the hull: complete gluing including the upper part
- Special care during the assembly of elements such as electronics to maintain a perfect seal of the rear walls
Security:
- Through-hull fittings close to the waterline (black water vents, sink) will be fitted with a valve.
- Rear cleats reinforced with a large counterplate for use with stragglers. If they are not accessible, tapped into an aluminium counterplate.
- Securing of the water heater by bolting or the use of reinforced tie-downs.
- Reinforced fuel tank stowage
- Reinforced stowage of fresh water tanks
- Raised installation of two bilge pumps
- Specific control of the mast and standing rigging by Z-Spars
- Stainless steel nuts to be fitted on all stainless steel deflectors
Wearing parts :
- All the sheaves of the rigging are made of aluminium
Reinforcements:
- Re-layering of the hull/deck connection at the bows
- Engine vent and BIB hatch plate laminated at the bottom
- Resumption of stratification of saffron yoke tubes
- No drilling in the hull for fixed portholes (plexi portholes removed)
- Structural reinforcement of subbarb chainplates
- Large aluminium counterplate for cleats, gennaker sheet block anchors and bow chainplates
- New mast base adapted to a less and more tolerant quest in case of very high load (less rigid)
Performance :
- New chainplate for the bowsprit, articulated on two axes to optimize the performance of downwind sails
- Preparation of the hull by sanding the gelcoat and smooth finishing of the keels and rudders.
- Trailing edge beveling to minimize vibration
- Stratification of the central gutter
- Flush treatment of the grounding anode
Autonomy:
- Installation of a watermaker in the port forward cabin
- AGM Batteries